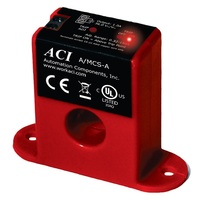
Welcome to Controls Traders, located in Adelaide, South Australia. We are a supplier of quality building automation controls and peripheral products for the HVAC industry. We stock a full range of controllers, sensors, valves and actuators, damper actuators and accessories to suit any application. Our aim is to provide our customers with the highest level of service, from sales to delivery and after sales support. With our extensive in-house knowledge and expertise in the industry, we can advise you on selection and application of our wide range of controls products.
Backed by 40 years industry experience. When you just need to be sure.
No, we’re serious. Anywhere. Anytime.
We stock all major global brands. And if we don’t have it, we’ll find it.
We warehouse the stock so you don’t have to wait.
$150.00 ex GST
Helpful guys over the counter, prompt responses and stock a wide variety of HVAC equipment. One of my go-to stores for parts and advise.
08/10/23
Huge range of HVAC controls readily available off the shelf with excellent customer service and knowledge amongst all staff!? If it's not on the shelf they can get it for you quick!
02/10/23
Great service, great products. The guys are always very helpful and will try to get whatever you need.
19/09/23
Have been using Control Traders for a while now. Peter and the team have been very helpful. Great prompt service
28/10/23
Have you ever tried plugging in your phone or hair dryer overseas, only to fry it within seconds? A voltage converter from our products range save your day in this case. Whether you’re charging gadgets, powering appliances, or switching between voltage systems, having a voltage converter is very important.
With the standard nominal voltage of 230 volts common in Australia, travelling with or importing devices often comes with voltage mismatches. In this article, Controls Traders explains how converters work, what to look for, and how to pick the right one for your needs.
A voltage converter, also called a power converter, is an electricity management appliance that changes electrical voltage into compatible voltage levels for devices. It ensures your appliances get the right amount of power, no matter where you are.
We have various forms of voltage converters, from step-up converters, which increase the input voltage, to step-down transformers, which decrease it.
A voltage converter works by stepping up or down to match your device’s needs. It’s like a translator for electricity, ensuring smooth power flow. HVAC systems use specific power supplies, for instance. A power converter ensures compatibility, especially in global installations.
Electrical devices work with specific voltages. When you plug a 230V device into a 120V socket, there’s not enough power to run the appliance.
Voltage converters come in different types. We'll break each down below:
An AC-to-DC converter transforms alternating current into direct current by allowing the flow of current in just one direction. It essentially "straightens" the current flow, working like a one-way valve for electricity.
Low-power devices like cell phones and laptops need DC electricity to run. But most outlets provide AC. The AC to DC voltage converter, or rectifier, converts AC from your wall socket to the DC your gadgets need.
In Australia, these converters are everywhere—from power banks to phone chargers. They’re a must-have if you’re travelling multiple countries with gear that relies on DC power.
A DC to AC voltage converter takes DC power (from car batteries, solar panels, to power banks) and turns it into AC.
If you’re off-grid with only a solar panel, an inverter lets you use regular appliances like laptops, dryers, or even a small coffee machine. For HVAC professionals, inverters are needed while working with off-grid or renewable power setups.
Australia runs on 50Hz electricity while the US uses 60Hz. You'll need a frequency converter or transformer if you’re using appliances or tools made for a different frequency.
For example, an imported HVAC unit may require a transformer to handle Australia’s power. It’s not just about voltage but also frequency compatibility.
A DC-to-DC power converter adjusts voltage levels between DC-powered devices.
For instance, powering multiple devices from a car battery, like GPS, dash cams, and phones, requires converting voltage down to match each device. Without it, you may damage your gear.
Choosing the right voltage converter is essential. At Controls Traders, we stock everything from rectifiers to transformers.
Adapters are like translators. They don’t change electricity, just the plug shape. For example, Australian outlets use a three-pronged plug. If your device is from the US, you’ll need a travel adapter to make it fit. But beware: travel adapters don’t adjust voltage.
Voltage converters, on the other hand, change the voltage to protect single-voltage devices like hair dryers or some power tools. Australia typically runs on 230 volts, but US appliances often run on 110 volts. Without a converter, that mismatch can fry your device.
The right power converter can save your gear from costly damages. Here are what to consider:
Start here. Check your device’s wattage needs. Hair dryers, for example, require up to 2000W. If your converter can’t handle it, you’ll be left with a fried appliance or no power at all.
If you’re running both low-power devices like toothbrushes and larger appliances, a dual voltage converter is what you need. It works with multiple devices at home and abroad.
Would you like to travel light? Then choose a converter that won’t weigh down your luggage. Compact units are perfect for globetrotters, whether you’re backpacking through Europe or jetting to Japan.
Power surges happen. Protect your gear with a converter that has a built-in surge protection. It’s a must for sensitive gadgets like laptops, tablets, and phones.
Planning trips to the USA, China, or Switzerland? A converter with multiple plug adapters helps you stay powered wherever you go.
Controls Traders is here to help. We stock reliable converters, power supplies, and HVAC products designed to meet Australian standards. Browse our range today and power your life. Or call us if you have any enquiries.
Use an adapter when your device is dual-voltage (check the power details on the label). Most modern gadgets, such as laptops, phones, and power banks, work with multiple voltages; they just need the right plug to fit the socket.
Use a power converter if your device is single-voltage (look for a number like "110V").
A voltage converter changes the voltage of electricity to suit your devices. For example, if you bring a 110V appliance from the US to Australia (which uses up to 240V), you'll need a converter to protect your device from getting fried. It’s essential for single-voltage gadgets.
Yes, but check the wattage of all the devices you plug in so you don't overload the converter. When trying to plug in your laptop, phone, and hair dryer at once, do the math. Overloading your converter could damage it—or, worse, your appliances.
That depends on your device. If it’s dual-voltage (e.g., 110-240V), you can use an adapter. However, check the label on your device. If it only says "110V" or "120V," get a converter.
Flip your device over and read the label. Look for something like "Input: 110-240V." This means your device can handle multiple voltages without a converter. However, you'll need a converter for single-voltage items like certain kitchen appliances or power tools.
Check out our range of voltage converters or contact us for further guidance on choosing a converter.
Read more
A Variable Speed Drive (VSD) is a vital tool for optimising the operation of electric motors across a wide range of industrial applications. These systems deliver precise speed control, ensuring electric motors run at their most efficient speed to meet specific load requirements. By enabling advanced motor control, variable speed drives reduce energy consumption, extend the life of mechanical equipment, and minimise operating costs.
Whether you're exploring what is a variable speed drive or looking to enhance energy efficiency, understanding the role of variable frequency drives (VFDs) is crucial for optimising operations.
A Variable Speed Drive is an electronic device that regulates the motor's speed by modifying the input voltage and frequency supplied to the motor. This ability to tailor motor performance ensures efficient operation at full speed, reduced speeds, or anywhere in between.
Variable frequency drives adjust the output voltage and frequency, enabling motors to meet changing demands without unnecessary energy use. Components like pulse width modulation (PWM) and voltage source inverters are key in achieving this accurate control.
For instance, in pump and fan applications, a variable speed drive pump reduces waste by ensuring the motor load matches the system's requirements, delivering optimal energy savings.
Traditional motors operate at a constant speed, consuming the same amount of energy regardless of the task's actual demands. This often leads to unnecessary electricity consumption and higher energy costs.
A variable frequency drive (VFD) enables motors to adjust their speed based on the load, delivering:
By installing variable speed drives, industries can achieve greater efficiency and reduce electricity consumption across operations.
Choosing the right speed drive is essential to meet specific operational needs. Several types of variable speed drives are designed to support various industrial applications.
AC drives are used with ac motors, including ac induction motors and synchronous motors. These drives adjust the output frequency and input voltage, making them ideal for applications requiring continuous operation, such as HVAC systems and manufacturing lines.
A dc motor variable speed drive is suitable for tasks requiring constant torque, such as conveyor belts or other heavy machinery. By regulating the dc voltage, these drives ensure reliable and efficient motor control.
Also called variable frequency drives, these devices are versatile, capable of handling both light and heavy loads. They optimise electric motors in pump and fan applications, using power electronics to achieve precise speed control and reduce electricity consumption.
Variable speed drives dynamically adjust the motor's speed to match demand, significantly reducing energy consumption. This capability is particularly valuable in systems with fluctuating loads.
Lower electricity consumption leads to reduced operating costs, helping industries save money while maintaining optimal performance.
By minimising mechanical stress and electrical stress, variable speed drives prolong the life of mechanical equipment, reducing maintenance needs and downtime.
Variable speed drives are used in a range of industries to improve efficiency:
By managing input voltage and output frequency, variable speed drives enhance the efficiency of electric motors, even in challenging conditions.
When choosing a variable speed drive, assess the following:
The next generation of variable speed drives focuses on sustainability and automation. Key advancements include:
Optimise your energy efficiency and reduce costs with the right variable speed drive. At Controls Traders, we provide expert advice to help you select the best solution for your specific industrial applications, whether you’re managing pump and fan applications, manufacturing systems, or renewable energy systems.
Visit Controls Traders for expert advice and tailored solutions to enhance your industrial systems.
A Variable Speed Drive adjusts motor speed to reduce energy consumption and optimise efficiency in industrial applications.
They match the motor’s speed to the required load, ensuring operations are performed at the most efficient speed.
AC drives control ac motors with variable loads, while DC drives provide steady torque for dc motors.
Focus on compatibility with the motor type, specific application needs, and potential energy savings.
Common problems, such as overheating, are often due to incorrect settings. Regular maintenance resolves these issues.
Read more
Have you ever noticed how your air conditioner blasts cold air at full-speed, even when it’s only mildly warm? That’s energy down the drain. Now, imagine if it could adjust itself, slowing down when needed, speeding up when necessary. That’s exactly what a Variable Frequency Drive (VFD) does in an HVAC system, often working alongside precision instruments from WIKA for accurate monitoring and control.
A VFD is a motor controller that regulates the speed of an electric motor by varying its frequency and voltage. Instead of running at full speed all the time, the motors only work as hard as they need to. That means lower energy consumption, less wear and tear, and better system performance. Let’s unpack it a bit more.
VFD stands for Variable Frequency Drive. It’s sometimes called an AC drive or adjustable speed drive, but the idea is the same. It controls how fast a motor spins.
So, how does it do that? A VFD tweaks both the frequency and voltage of the electricity going to a motor. The lower the frequency, the slower the motor. The higher it is, the faster it runs.
Now, you might’ve heard of a Variable Speed Drive (VSD) and wondered, “Isn’t that the same thing?” Not quite. A VSD refers to any device that changes a motor’s speed, while a VFD specifically does it by adjusting frequency and voltage.
Think of it like this—every VFD is a VSD, but not every VSD is a VFD. It’s like how all squares are rectangles, but not all rectangles are squares.
Now, let’s go into how a VFD actually works.
Have you ever left a tap running full blast when you only needed a trickle? That’s what happens when an HVAC system runs at full speed all the time. It wastes energy.
A Variable Frequency Drive (VFD) fixes this by adjusting motor speed to what's needed. It changes the frequency and voltage of the electricity supplied to the electric motor, letting it speed up or slow down as needed.
When demand is low, the motor slows down, using less power. When more airflow or cooling is needed, it speeds up. This speed control cuts energy consumption, improves efficiency, and reduces wear on equipment. In fact, HVAC systems with VFDs can slash energy use by up to 50%, which is great for both the environment and your power bill.
A VFD isn’t just a black box that magically saves energy. It has four key parts working together to control motor speed:
Together, these components make sure the electric motor runs only as hard as it needs to—no more, no less.
Think about an office building on a mild spring day. The aircon doesn’t need to work as hard, but without a VFD, it still runs like it’s the middle of summer, which is wasteful, right?
With a variable frequency drive, the system slows down when cooling demand drops and ramps up when needed. That means better efficiency, lower costs, and longer-lasting equipment.
HVAC systems consume a massive chunk of a building’s electricity, up to 70% in some cases. Running them at full speed all day is like driving a car with your foot flat on the accelerator, even when you're in traffic.
A variable frequency drive (VFD) solves this by adjusting motor speed to match demand. Less power wasted means lower energy bills. In commercial buildings, VFDs can cut electricity costs by 30% to 50%, which adds up fast.
Have you ever heard an old aircon unit rattle and shake when it kicks on? That’s the strain of starting at full power. It wears down components and leads to breakdowns.
With a VFD, motors start up gradually, reducing stress on motor windings and driven equipment. That means less maintenance, fewer breakdowns, and a longer lifespan for HVAC systems.
It’s simple: less strain, fewer repairs, more savings. That’s why we recommend that VFDs be used in modern HVAC systems.
Picking the right variable speed drive (VSD) for your HVAC system isn’t just about power. It’s about efficiency, longevity, and cost savings. Get it wrong, and you could be dealing with overheating motors, higher energy bills, or unnecessary breakdowns. So, how do you choose the best one?
Size matters, especially with variable frequency drives (VFDs). Choose wrong, and you’re either overloading your system or wasting money on an oversized unit. Here’s what to consider:
For example, in a commercial building, a VFD running an AC induction motor might need pulse width modulation (PWM) for smoother operation. No one wants a jerky airflow system.
Installing a variable frequency drive VFD is not rocket science, but get it wrong, and you’ll be calling an electrician more often than you’d like.
Here’s how to get it right:
Note: A well-maintained variable frequency drive can last 10+ years, keeping your HVAC system running efficiently.
Not all VFDs are the same. Some last longer, run smoother, and offer better energy savings. Here are the top brands trusted in Australia:
Need a reliable VFD or AC drive for your HVAC system? Check out Controls Traders in Adelaide. We stock high-quality drives from Danfoss to Siemens and more.
A variable frequency drive does more than just control motor speed. It reduces energy consumption, extends motor life, and keeps your HVAC system running smoothly.
Choosing the right VFD means fewer breakdowns, lower power bills, and a more comfortable space. So whether you’re managing an office, shopping centre, or industrial plant, a well-sized variable speed drive is a smart investment.
Need help finding the best VFD? You can shop for them here at Controls Traders on our dedicated store for variable speed drives.
There are three main types of variable frequency drives (VFDs)—Voltage Source Inverter (VSI), Current Source Inverter (CSI), and Pulse Width Modulation (PWM). VSI is the most common and works well for HVAC systems. CSI is used in heavy-duty industrial settings, while PWM provides the smoothest speed control, reducing noise and making motors run more efficiently.
A Programmable Logic Controller (PLC) is like the brains of an operation, while a VFD is the muscle. A PLC manages different system processes, like turning fans on and off or adjusting airflow. A VFD is a type of AC drive that controls the speed of the motor, making sure it runs at just the right level instead of wasting energy.
A VFD is made for AC motors, especially AC induction motors. It takes incoming AC power, converts it to DC voltage, then turns it back into AC power at different frequency and voltage levels. This lets the system fine-tune motor speed, helping save energy and extend the life of the equipment.
An inverter changes DC power into AC power, like what you’d see in solar or backup battery systems. A VFD, on the other hand, is a type of motor controller that drives an electric motor by tweaking frequency and voltage. This means a VFD doesn’t just convert power—it actively controls how fast a motor runs, making it perfect for HVAC and industrial systems.
In a VFD system, frequency and voltage work together to set the speed of the motor. More frequency and voltage means faster speed. Less means slower. This speed control is what makes variable frequency drives so useful—they adjust power based on demand, cutting down on energy consumption and preventing unnecessary wear and tear.
Got more questions or need help choosing a VFD? Send us a message or call us at 1300 740 140
Read moreThe Suction Control Valve (SCV) is a crucial component in HVAC systems, regulating refrigerant flow and pressure to maintain optimal performance. It ensures precise control of refrigerant circulation, preventing over- or under-supply that can affect efficiency. A malfunctioning SCV can lead to inconsistent airflow, reduced cooling or heating capacity, and increased energy consumption—issues that can be addressed with quality components from KTS.
A suction control valve regulates refrigerant flow and pressure in an HVAC system. Located within the compressor, it adjusts suction levels to maintain optimal system performance.
Key benefits of a well-functioning SCV include:
Identifying suction control valve issues early can prevent costly HVAC system failures. Common signs include:
Identifying suction control valve issues early can prevent costly HVAC failures. Common signs include irregular airflow, frequent short cycling, higher energy consumption, unexpected shutdowns, and reduced cooling or heating efficiency. Addressing these issues promptly helps maintain optimal system performance.
Suction control valve failures in HVAC systems often result from:
To test a suction control valve, follow these steps:
Suction control valve failures in HVAC systems often result from:
A new SCV installed with these precautions ensures reliable fuel pump operations and optimal engine performance.
Consult a professional if you notice persistent suction control valve symptoms such as rough idling or poor acceleration on your HVAC.
Regular maintenance, using high-quality refrigerant, and monitoring suction control valves are essential for optimal HVAC system performance. Addressing issues early helps prevent costly repairs and system failures. Persistent symptoms should be diagnosed by an HVAC professional, with replacement considered if necessary.
If you’re experiencing suction control valve issues or need a reliable replacement, explore high-quality SCV options and expert assistance at Controls Traders. Keep your HVAC system running efficiently with trusted solutions tailored to your needs.
A faulty suction control valve in an HVAC system can cause inconsistent airflow, frequent short cycling, higher energy consumption, unexpected shutdowns, and reduced cooling or heating efficiency. If these issues persist, professional inspection and possible replacement may be needed.
To test your suction control valve in an HVAC system, monitor pressure readings for irregularities, listen for unusual noises, and check for inconsistent airflow. If issues persist, a professional technician can perform diagnostic tests and calibrate or replace the valve if necessary.
A suction control valve in an HVAC system can fail due to wear and tear, refrigerant contamination, electrical issues, or lack of regular maintenance. These factors can lead to improper refrigerant flow, reduced efficiency, and system malfunctions.
A suction control valve in an HVAC system is typically replaced rather than repaired as internal components wear out or become contaminated over time. If the valve is malfunctioning, a professional technician can assess whether cleaning or calibration is possible, but replacement is often the most effective solution.
A suction control valve in an HVAC system is usually replaced rather than repaired, as wear, contamination, or electrical issues can affect its performance. Seek professional help if you notice inconsistent airflow, short cycling, high energy consumption, or system shutdowns to prevent further damage.
Read moreSign up by email to receive inspiration, product updates and special offers from our team.
Welcome to our website. If you continue to browse and use this website, you are agreeing to comply with and be bound by the following terms and conditions of use, which together with our privacy policy govern Controls Traders Pty Ltd’s relationship with you in relation to this website. If you disagree with any part of these terms and conditions, please do not use our website.
The term ‘Controls Traders Pty Ltd’ or ‘us’ or ‘we’ refers to the owner of the website whose registered office is 40 Stepney Street, STEPNEY SA 5069. Our ABN is 21 610 375 365. The term ‘you’ refers to the user or viewer of our website.
The use of this website is subject to the following terms of use:
This privacy policy sets out how we uses and protects any information that you give us when you use this website.
We are committed to ensuring that your privacy is protected. Should we ask you to provide certain information by which you can be identified when using this website, then you can be assured that it will only be used in accordance with this privacy statement.
We may change this policy from time to time by updating this page. You should check this page from time to time to ensure that you are happy with any changes.
What we collect
We may collect the following information:
What we do with the information we gather
We require this information to understand your needs and provide you with a better service, and in particular for the following reasons:
Security
We are committed to ensuring that your information is secure. In order to prevent unauthorised access or disclosure, we have put in place suitable physical, electronic and managerial procedures to safeguard and secure the information we collect online.
How we use cookies
A cookie is a small file which asks permission to be placed on your computer's hard drive. Once you agree, the file is added and the cookie helps analyse web traffic or lets you know when you visit a particular site. Cookies allow web applications to respond to you as an individual. The web application can tailor its operations to your needs, likes and dislikes by gathering and remembering information about your preferences.
We use traffic log cookies to identify which pages are being used. This helps us analyse data about webpage traffic and improve our website in order to tailor it to customer needs. We only use this information for statistical analysis purposes and then the data is removed from the system.
Overall, cookies help us provide you with a better website by enabling us to monitor which pages you find useful and which you do not. A cookie in no way gives us access to your computer or any information about you, other than the data you choose to share with us.
You can choose to accept or decline cookies. Most web browsers automatically accept cookies, but you can usually modify your browser setting to decline cookies if you prefer. This may prevent you from taking full advantage of the website.
Links to other websites
Our website may contain links to other websites of interest. However, once you have used these links to leave our site, you should note that we do not have any control over that other website. Therefore, we cannot be responsible for the protection and privacy of any information which you provide whilst visiting such sites and such sites are not governed by this privacy statement. You should exercise caution and look at the privacy statement applicable to the website in question.
Controlling your personal information
You may choose to restrict the collection or use of your personal information in the following ways:
We will not sell, distribute or lease your personal information to third parties unless we have your permission or are required by law to do so. We may use your personal information to send you promotional information about third parties which we think you may find interesting if you tell us that you wish this to happen.
If you believe that any information we are holding on you is incorrect or incomplete, please write to or email us as soon as possible at the above address. We will promptly correct any information found to be incorrect.